Center for Rational Catalyst Synthesis (CeRCaS)
June 17, 2020
Improvements in direct-methanol fuel cells (DMFCs) have been achieved at the Univ. of South Carolina based on a new, easy-to-scale method to synthesize bimetallic catalysts.
The two most common types of fuel cells being developed for mobile transportation applications are DMFCs and hydrogen fuel cells. Methanol is safer than hydrogen, and it is easier to handle and install in refueling stations. Whereas a monometallic platinum (Pt) catalyst may be used for H2 fuel cells, a more-expensive bimetallic catalyst — typically consisting of Pt and ruthenium (Ru) — is required for DMFCs.
In a DMFC, methanol oxidation takes place at the anode. During methanol oxidation, the intermediate carbon monoxide (CO) is formed, which strongly adsorbs on the Pt surface, reducing the number of available reaction sites and thus the performance of the cell. Ru helps to counteract this effect by acting as an adsorption site for H2O. The H2O reacts with adsorbed CO to form CO2 and H2, the desired product. In theory, metals such as cobalt (Co) and nickel (Ni) could serve as less-expensive alternatives to Ru.
In order for bimetallic catalysts to be effective, the two metals must be in close contact. However, the most common way to make these catalysts, a process termed co-impregnation, is unable to do this effectively. During co-impregnation, metal nanoparticles are deposited on the surface of a substrate. The quantity, size, and distribution of the deposited nanoparticles are difficult to control. And, achieving co-impregnation without segregation of the two metals is nearly impossible.
With funding from the National Science Foundation (NSF), chemical engineers at the Univ. of South Carolina have developed a simple, effective, generalizable method for the synthesis of supported bimetallic nanoparticles in which the two metals are intimately alloyed and the size of the nanoparticles can be precisely controlled. This method is called co-electroless deposition (co-ED).
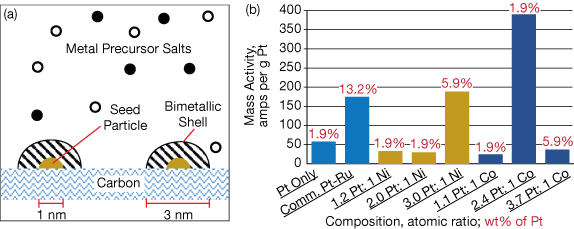
The new process (Figure 1a) employs precision flow delivery of metal precursor solutions into a reactor with a solution of a reducing agent such as dimethylamine borane (DMAB). The metals in the precursor solutions are quickly and completely reduced on the surface of pre-deposited metal seed particles that are attached to a carbon support layer. The metals form an evenly distributed bimetallic shell around the seed particles. The thickness and composition of the shell is determined by the amounts and rates of metals being deposited.
Previous computational studies predicted optimal atomic ratios of Pt-Co and Pt-Ni catalysts, but these ratios had largely been untested due to the difficulties of preparing bimetallic catalysts with uniform compositions. The UofSC team created and validated several of these catalyst compositions.
The engineers chose palladium nanoparticles as their seed particles, although any catalytic metal (e.g., Ni, Cu, or Ag) can be used. They created several Pt-Ni and Pt-Co bimetallic catalysts with varying atomic ratios and weight percentages of Pt (Figure 1b). Each catalyst was evaluated using cyclic voltammetry (CV).
Testing showed that a few of their catalysts had substantially higher mass activities (i.e., useful power) than a conventional Pt catalyst and a commercially available Pt-Ru catalyst. In fact, a Pt-Co catalyst with an atomic ratio of 2.4:1 was more than twice as active than the commercial benchmark catalyst and it used only 0.24 wt% Co, at 1/7,000th of the cost of Ru.
The co-ED technique can be extended to chemical catalyst applications and applied to substrates other than carbon, such as silica, titania, and alumina. By precisely controlling the thickness of the bimetallic shell, co-ED enables less metal to be used in production of bimetallic catalysts, which will help lower their cost. Reducing the costs of bimetallic catalysts will be critical in making DMFCs viable for automobiles. Most importantly, co-ED is straightforward, versatile, and can be easily scaled for larger applications.
This research was funded through the NSF Industry-University Cooperative Research Centers Program (IUCRC) and an NSF Chemical, Bioengineering, Environmental and Transport Systems (CBET) award.
This article was prepared by NSF for AIChE and appeared in the April 2019 issue of Chemical Engineering Progress.