Center for Resource Recovery and Recycling (CR3)
August 31, 2021
A method to improve metal production has just been developed by researchers funded by the National Science Foundation's (NSF) Industry-University Cooperative Research Center (IUCRC) – Center for Resource Recovery & Recycling (CR3) – at the Worcester Polytechnic Institute and the Colorado School of Mines with an international site at KU Leuven, Belgium.
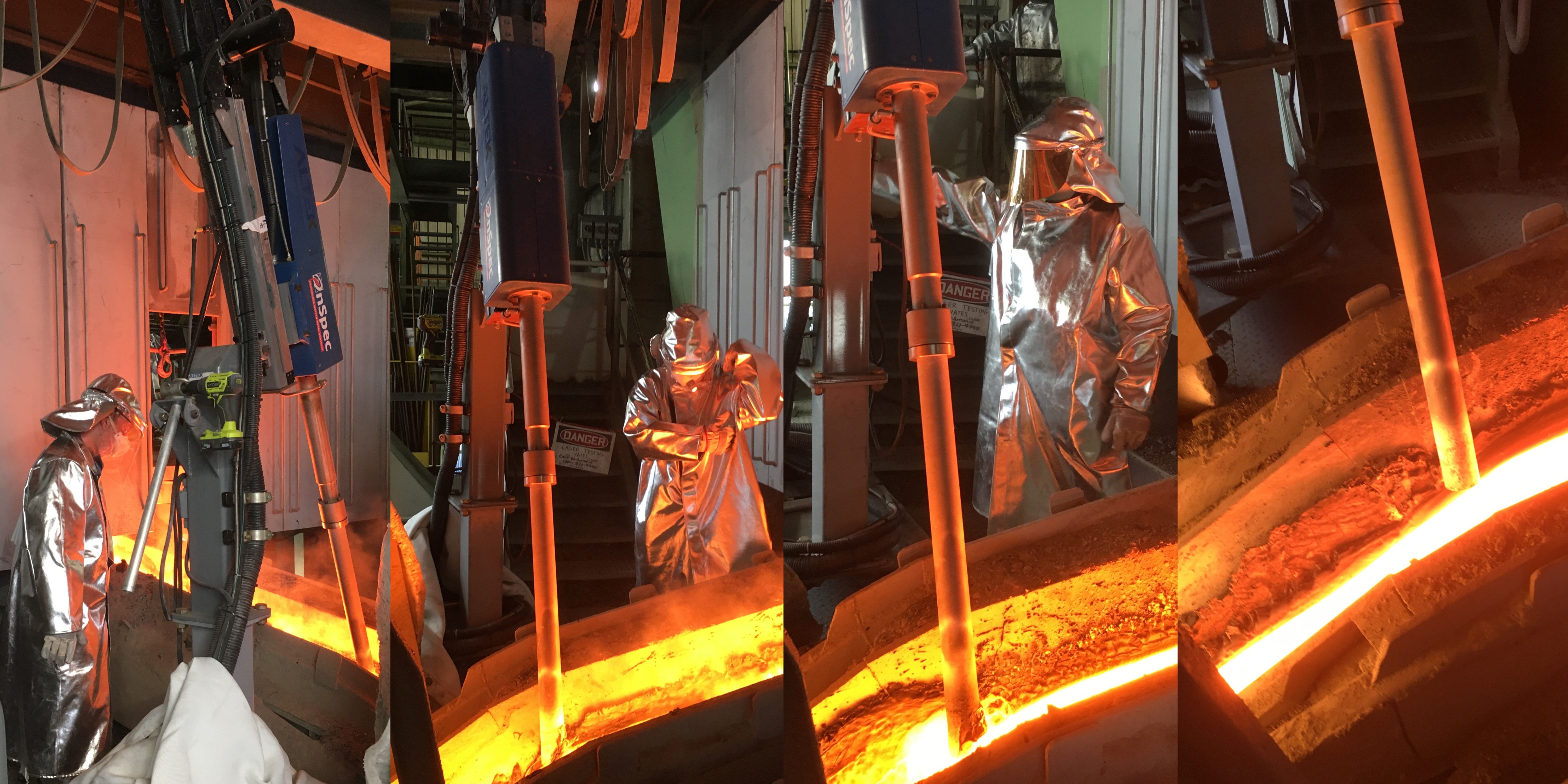
While previous techniques required removing molten metal for testing elsewhere, the new technique directly measures a remnant by-product of metal production called slag without it needing to be removed—reducing the analysis process down from a half hour to just minutes. Ultimately, this will reduce fossil fuel consumption in metal production as well as save time and money.
In a metallurgical furnace, where ores are processed into refined metals, the pure molten metal sinks to the bottom, leaving the unwanted slag at the top. The new technique can directly measure the slag in the furnace, which is then used to infer how close the metal product is to being pure. In addition to saving metal workers the long process of removing the metal to be tested elsewhere, the new system allows engineers to know precisely when the metals are ready, saving the additional fuel that is sometimes needed to post-process materials taken out of the furnace too early.
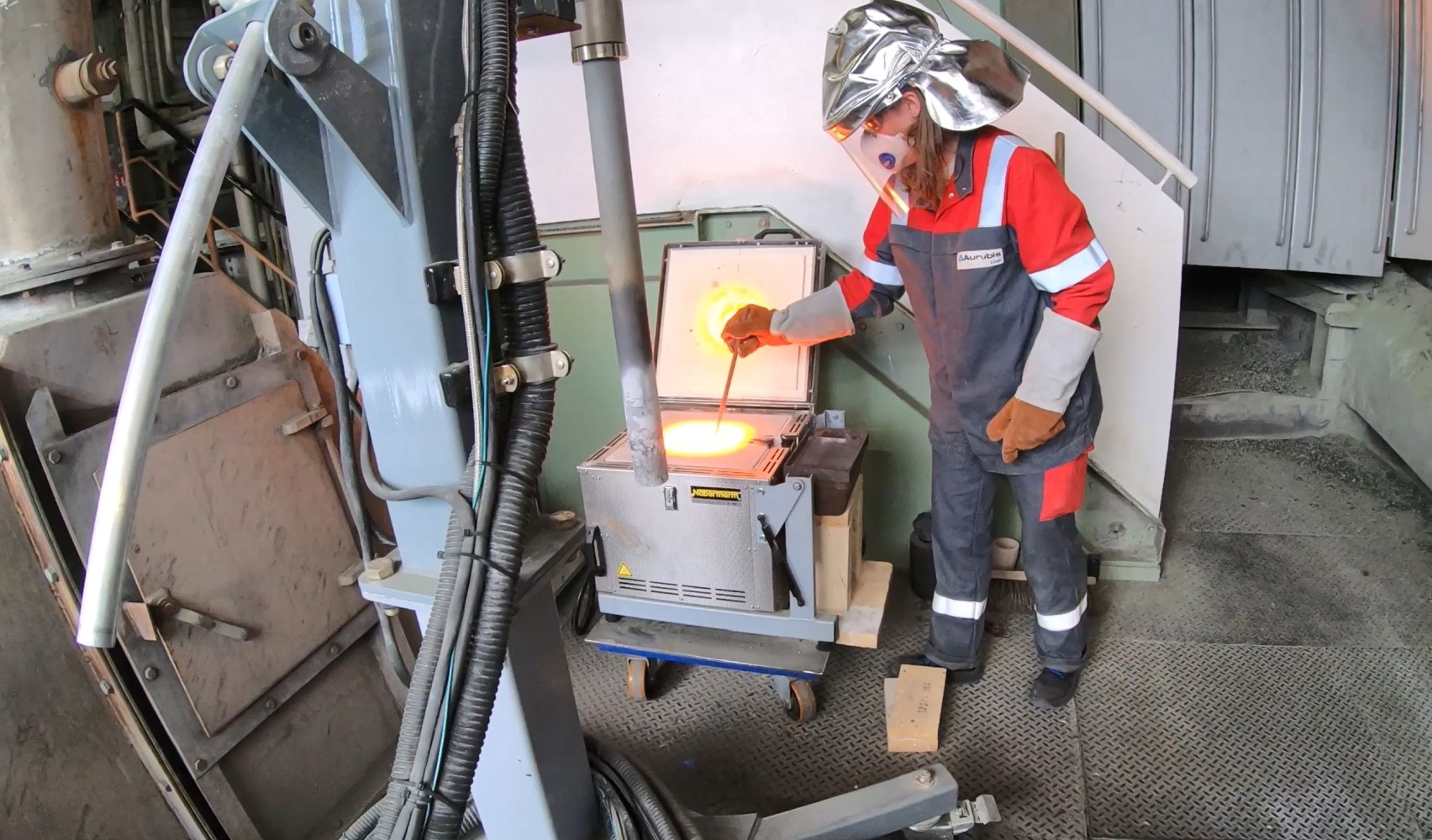
The innovative technique is known as laser-induced breakdown spectroscopy, or LIBS. LIBS uses a laser beam that pulses short bursts lasting just fractions of a second directed at the material. The high-energy laser turns a tiny bit of the material into a glowing plasma whose light can be measured with a spectrometer and a detector. In a calibrated system, this can give the composition of the metal within minutes. LIBS improves the feedback process by providing metal workers with near real-time information on the composition of the metal. This allows them to know when the product is ready for the next step.
"It is a rather simple set up," said Elise François, a doctoral candidate at KU Leuven who heads the project. "What is special about this technique is that you can apply it without removing material from production, and you can tailor it to your application."
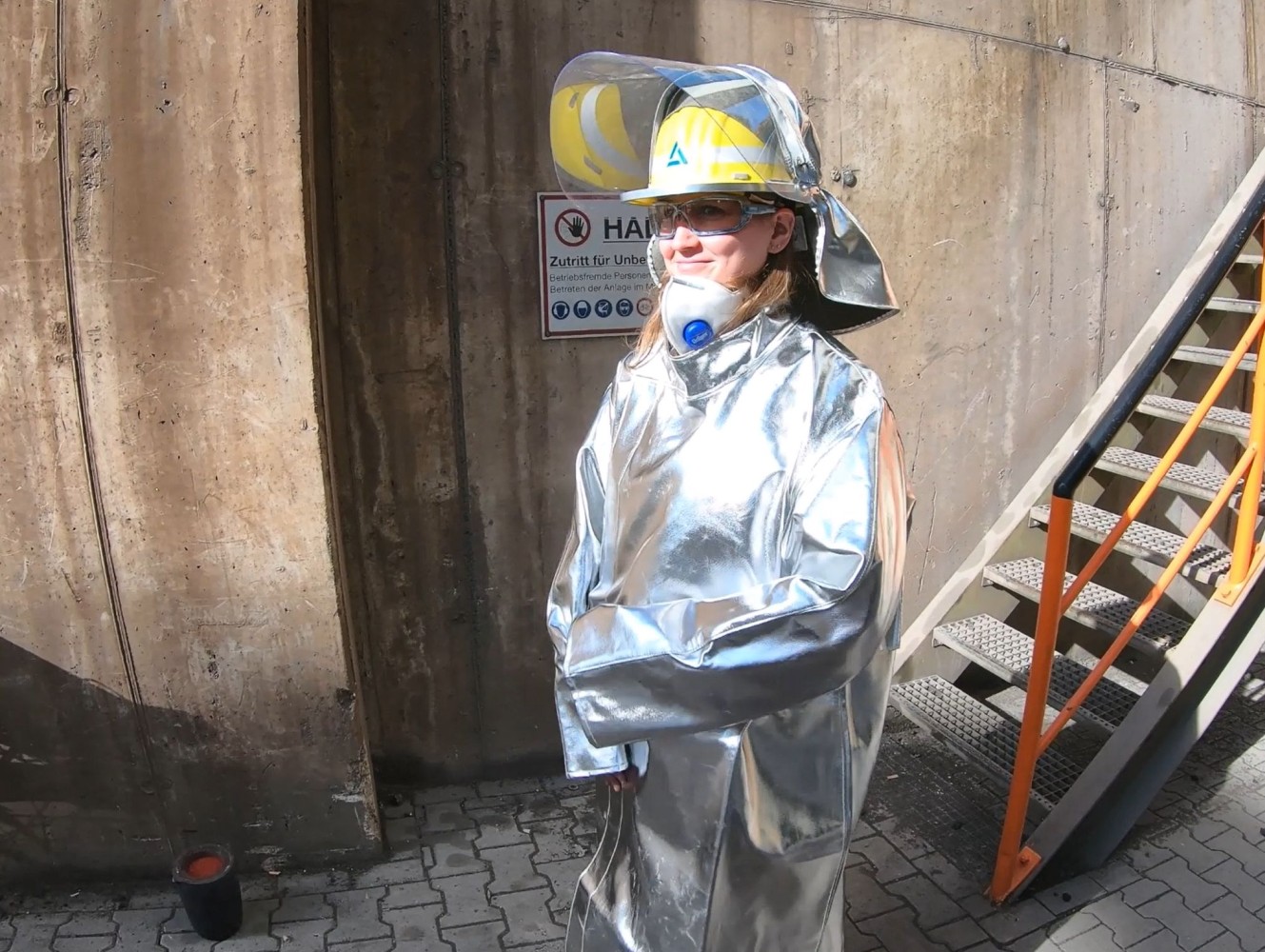
Traditionally, the analysis of the metal is done with x-ray fluorescence, which requires removing a sample of the metal from the production line. The removed sample, after being cooled, milled and homogenized, is bombarded with x-rays. The energized material then re-emits new x-rays that reveal the chemical nature of the material. The whole process can take 20 to 30 minutes—at which point the product in the furnace can have a different composition than the sample removed for testing. As a result, metallurgists are constantly working with old information.
"This time delay means that the engineers have to make on-site decisions with old information," François said.
Previously, on-line LIBS technology has been typically used to identify and sort scrap material. The technology was successfully demonstrated at WPI in CR3 on an earlier project on 'Auto-Al Scrap Material Flow Analysis with Compositional Projections' employing LIBS. An industrial member of CR3, ERCo, provided the experimental LIBS facility. François' new method builds on that technology, extending it to the more complex compositions found in slag, which often contain a multitude of different elements in unknown concentrations. François developed a calibration method that allows easy identification of major components of the slag on-line, like iron-, silicon- and aluminum-oxides.
In contrast to x-ray fluorescence, LIBS can detect light elements like carbon and phosphor. Currently, the system is highly successful in on-line applications in identifying elements in concentrations above 2%. Methods to quantify minor components on-line under 2 percent are being developed, which will help further improve the precision of the metal refining.
The calibration method was initially developed in a laboratory setting but François was able to test the system in an industrial setting. An industrial demonstration of the technology was undertaken at one of the CR3 industry member's facilities in Europe that was supported by four other center members in a collaborative effort. ERCo provided the LIBS equipment for this study.
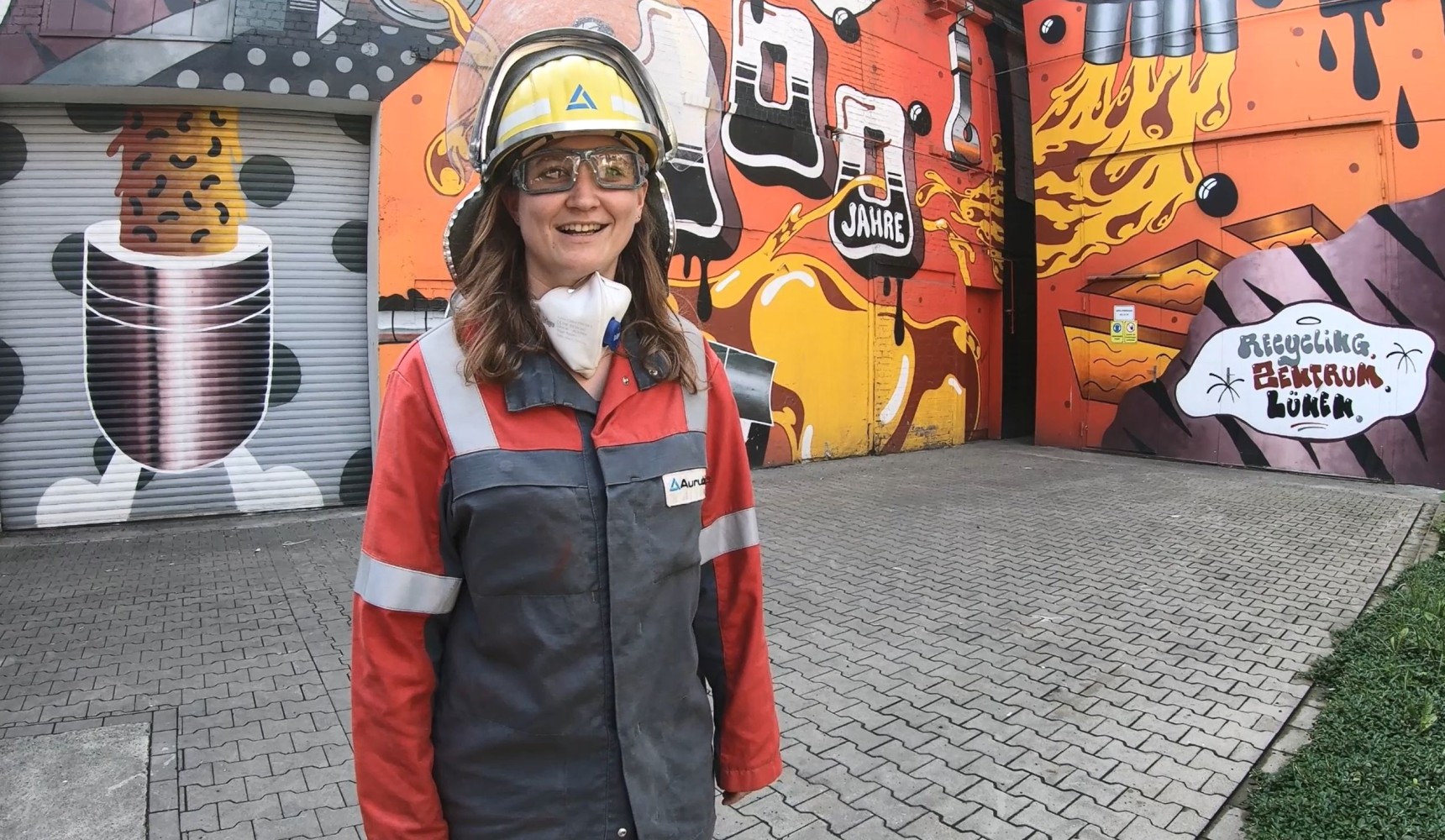
With on-line slag measurements now effectively demonstrated, it will not be long before large-scale industrial implementation is possible.
Thanks to the funding and support from the NSF's IUCRC CR3 program, which enables scientists and engineers to further investigate cutting-edge research of interest to industry, this commercially useful method has been applied in industry. "Without NSF, we would not have been able to bring all these industrial partners together with universities," François said.